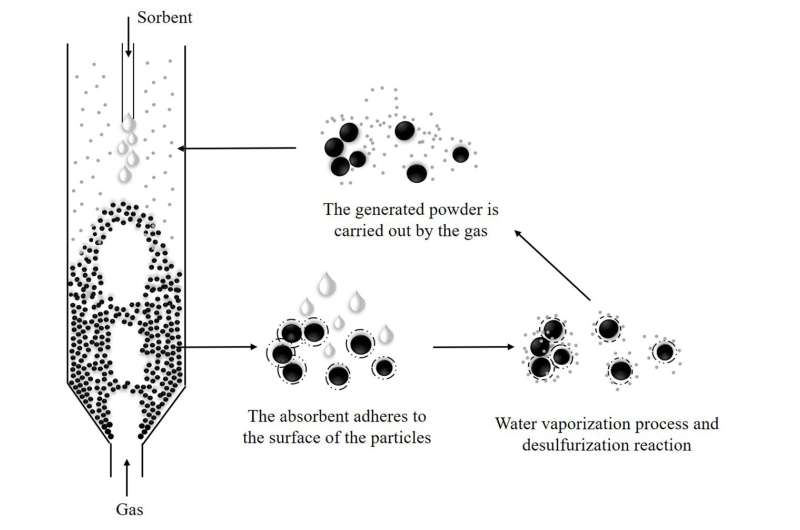
Sulfur dioxide is the main source of air pollution and easily forms a haze deteriorating the air quality. Therefore, various studies on the reduction of sulfide emissions generated during fossil combustion have been performed. Among them, the semi-dry flue gas desulfurization technology in powder-particle spouted beds (PPSBs) is considered a reliable and effective desulfurization method.
With the development of computational fluid dynamics (CFD) methods, an increasing number of researchers conducted numerical simulations of the desulfurization of semi-dry flue gas in a spouted bed. Such a bed involves a multiphase flow and heat and mass transfer, including a gas-solid two-phase flow, a water vaporization process, and a desulfurization reaction. However, the current homogeneous drag models (such as the Gidaspow and Wen-Yu ones) used in simulations did not consider the influence of the mesoscale structure during drag coefficient calculations, resulting in a severe overestimation of the drag, which had a negative impact on simulation accuracy. To solve this problem, Feng Wu and his team modified the heterogeneous gas-solid drag model and applied it to the simulation of the two-dimensional spouted bed. The relevant work was published online in Frontiers of Chemical Science and Engineering on December 9, 2021.
In this study, by simulating and analyzing the gas-solid two-phase flow coupled water vaporization and desulfurization process of the spouted bed, they found that the adjusted mesoscale drag model can accurately and effectively describe the semi-dry flue gas desulfurization process in the spouted bed. There is a structure activity relationship between the drag model and the heat transfer, mass transfer and desulfurization reaction.
The obtained results revealed that the particle velocity simulated by the modified mesoscale model is more consistent with the experimental data. The spout morphology simulated by the adjusted mesoscale drag model was unstable and discontinuous bubbling spout unlike the stable continuous spout obtained using the Gidaspow model. The bubbling spout state conforms to physical reality.
The water distribution in the spouted bed simulated by the EMMS drag model was uniform, and its water vaporization rate was larger than that determined by the Gidaspow drag model. The mass fraction of water in the gas at the outlet obtained by the heterogeneous drag model was 1.5 times greater that estimated by homogeneous drag model during the simulation of water vaporization.
For the desulfurization reaction, the experimental desulfurization efficiency was 75.03%, while the simulated desulfurization efficiencies obtained by the Gidaspow and adjusted mesoscale drag models were 47.63% and 75.08%, respectively, indicating much higher accuracy of the latter technique.
Feng Wu and his team will further expand the adjusted mesoscale drag model to three dimensions in order to obtain more relationships between drag models and heat and mass transfer.
Xinxin Che et al, Effect of adjusted mesoscale drag model on flue gas desulfurization in powder-particle spouted beds, Frontiers of Chemical Science and Engineering (2021). DOI: 10.1007/s11705-021-2100-8
Provided by
Higher Education Press
Citation:
More accurate modeling of flue gas desulfurization in powder-particle spouted beds (2022, February 28)
retrieved 28 February 2022
from https://phys.org/news/2022-02-accurate-flue-gas-desulfurization-powder-particle.html
This document is subject to copyright. Apart from any fair dealing for the purpose of private study or research, no
part may be reproduced without the written permission. The content is provided for information purposes only.