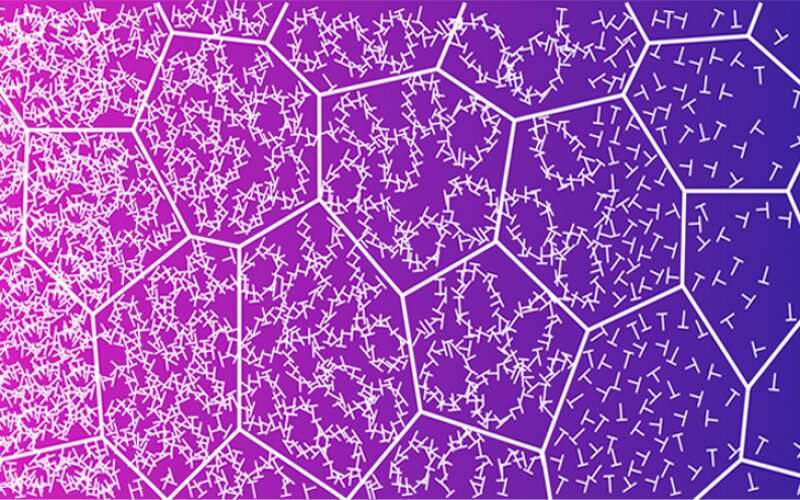
Researchers at Oak Ridge National Laboratory have developed a method of adding nanostructures to high-entropy metal alloys, or HEAs, that enhance both strength and ductility, which is the ability to deform or stretch under tensile stress without failing.
The results, published in Science, open a promising pathway for tailoring HEA properties using small gradient structures to produce improved high-performance metals for a wide range of applications.
Conventional metallic materials, including HEAs (metals composed of five or more elements), become less ductile or more brittle as their strength increases.
The scientists used neutron diffraction methods at ORNL’s Spallation Neutron Source to confirm tiny defect features, called stacking faults, form easily in an HEA compared to conventional fine-grained alloys.
“The stacking faults enhanced the test alloy’s plasticity while also contributing to increased strength and hardening,” said ORNL’s Ke An. “Industries that could greatly benefit include automotive, power distribution and aerospace.”
Qingsong Pan et al, Gradient-cell–structured high-entropy alloy with exceptional strength and ductility, Science (2021). DOI: 10.1126/science.abj8114
Citation:
Using neutrons to analyze modified high-entropy metal alloys (2021, November 2)
retrieved 2 November 2021
from https://phys.org/news/2021-11-neutrons-high-entropy-metal-alloys.html
This document is subject to copyright. Apart from any fair dealing for the purpose of private study or research, no
part may be reproduced without the written permission. The content is provided for information purposes only.